Training Session #14E – SMARTScan Startup
Definitions:
- 9+4 Box ID – is the specific purchase order item record being received
-
- The Vendor Code, SYND above, is the Source Entry associated with the Vendors information
- Backstock - The Backstock location is where the Receiving Manager receives products using the “Add to Back Stock” app in SMARTScan Tools.
- GTIN – Global Trade Item Number is a 14-digit number.
- MID – Manufacturers’ Identification Numbers catalog, track, and control their products.
- SKU – Stock Keeping Unit, pronounced “skew,” is an identification number representing your internal Product Code, a UPC, GTIN, Manufacturers Code (MID), or the Vendors Primary Product Code.
- UPC – Universal Product Code is a 12-digit number to standardize inventory tracking. The newest UPCs are 13 digits and must be stored in the GTIN field.
- Zebra TC – Zebra Touch Computer.
Overview:
SMARTScan™ Tools is our software suite of bar code scanning programs designed to run on the latest technology devices, the Zebra TC21 (Wi-Fi only) or TC26 (Wi-Fi or Cellular) series of handheld scanners.
Using these scanners and our suite of specially designed programs will improve your operating efficiency, reducing errors and ensuring accuracy using your internal Wi-Fi or external cellular networks.
There are 8 SMARTScan™ Tools fully developed and ready for your use today.
SMARTScan options include:
The first program is SMART Scan to do physical inventory counts and reconciliation.
- Product Lookup, see the screen below, is used to do price checks, show quantity on-hand and Product locations. Prints shelf price labels
- Order Entry to create a Sales Order by selecting the customer and scanning bar codes
- Inventory Receiving (Receives PO Items by 9+4 Box ID, see picture below)
- Location Quantity Management
- Production Receiving (Receives 1 box directly into inventory for each scan)
- Order Validation with Sales Order for products shipped
- Pallet Receiving
For example, below is a screenshot of the Product Lookup Screen with the option to print bar code labels:
There are specific videos for your review on how to use the SMARTScan Tools. You can access these videos via our Floral Computer Systems Website, select the Support Tab, and click Knowledge Base Videos:
https://floral-computer-systems.helpscoutdocs.com/category/37-smartscan
Specific workflow objectives of the SMARTScan tools are:
- Inventory counts from one or multiple locations
- Create a customer sales order by scanning a product code or 9+4 bar code on receiving labels
- Identify Product location and quantities at that location
- Product Receiving using bar codes
- Sales Order Verification before shipping
- Pallet Receiving
- Product Lookup by scanning a bar code to see:
a. SKU
b. Product Code
c. Product Description
d. UPC
e. Location of Product
f. Pack
g. Quantity On Hand
h. Make quantity adjustments
i. Quantity On Hold
j. Net Available
k. Price
l. Print Labels with the option to show the price
- Remotely, using the handheld scanner, make inventory adjustments.
- Prepare to get Started:
To get started, once your SMARTSystem is installed, you need specific equipment setup and software operational:
- 1. Wi-Fi to cover the warehouse, coolers, and display areas
- 2. A bar code label printer, printing either 4” x 3” or 6” x 4” labels
- 3. Label stock for 4” x 3” labels, recommended
- 4. Install the SMARTScan Software programs
- 5. Set the SMARTSystem to print the 4” x 3” uniquely designed label.
- System Control, Purchasing Options menu, set the Receiving Label Type:
Example of SMARTScan Receiving Label
- a. The top bar code is to receive products and update the exact line item in your purchase order.
- b. The bottom bar code is the product code used for all other scanning requirements.
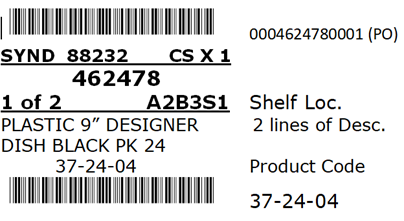
Setup Shelf Locations:
Product locations enhance managing your inventory counts. You may want to review the design of SMARTSystem “Management Training 14D - Warehouse Workflow Defined for Receiving.”
SMART Scan will help you identify product locations in Backstock and Display areas.
Aisle, Bay, and Shelf locations usually identify a Backstock area where most of your products are stored. Product Lookup will show the location of each product and other information.
Review your warehouse area and determine your locations, like: Aisle, Bay and Shclf. Using the Inventory Shelf Location Maintenance and Labels program on the Inventory Menu, print the bar code labels that are used in SMARTScan to identify locations:
Label your product locations using this program:
Inventory Menu > Inventory Shelf Location maintenance and Label Printing
See another example of your warehouse locations shown in the Inventory Location View below:
References:
- Management Training #14A – Hard Goods Scanning to Input Balance Flow Chart
- Management Training #14B - SMARTScan Bar Code Physical Inventory Counts
- Management Training #14C - SMARTScan Physical Inventory Control
- Management Training #14D -Warehouse Workflow Defined for Receiving